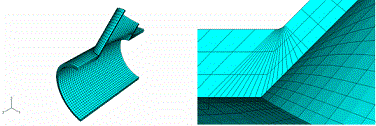
目前,管材滾彎加工在航空航天、汽車、船舶制造等工業(yè)中應(yīng)用十分廣泛,對管材彎曲技術(shù)和質(zhì)量的要求也越來越高。但是,由于管材具有特殊的中空結(jié)構(gòu)以及受多種非線性因素的影響,在滾彎成形時極易產(chǎn)生失穩(wěn)、起皺和開裂等問題。對上述問題的研究單純依靠實驗的方法所需周期較長、費(fèi)用高,且試驗過程中的隨機(jī)干擾因素較多,難以對工藝參數(shù)通過試驗進(jìn)行改進(jìn)和提高。
近年來,計算機(jī)仿真技術(shù)的發(fā)展為塑性成形研究提供了有力的輔助工具,各種有限元分析計算方法在管材彎曲變形研究中也得到了廣泛應(yīng)用,并已在彎曲加工類產(chǎn)品的設(shè)計和優(yōu)化等方而被證明是有效的。在管材滾彎工藝研究中,將有限元模擬技術(shù)與實驗結(jié)合起來對彎曲變形過程中的諸多現(xiàn)象進(jìn)行比較分析,對成形過程進(jìn)行科學(xué)預(yù)測,并對工藝加以優(yōu)化,已成為人們關(guān)注的問題。
本研究通過對薄壁不銹鋼管件的彎曲成形過程進(jìn)行三維彈塑性有限元模擬,揭示了其成形時應(yīng)力應(yīng)變分布規(guī)律和變形機(jī)理,分析了對成形質(zhì)量影響的主要因素,為進(jìn)一步研究薄壁不銹鋼的變形機(jī)理和失效機(jī)理奠定了基礎(chǔ),為同類產(chǎn)品彎曲成形工藝的制定及工藝參數(shù)的優(yōu)化提供指導(dǎo)。
模擬主要針對小直徑小鑄鋼管件的回轉(zhuǎn)式滾動彎曲變形。實驗用管件外徑為小12mm,彎模半徑為R30 mm,管件壁厚為t=1.2 mm;實驗設(shè)備為自制手動彎管機(jī)。彎曲成形前,應(yīng)對管材形狀、尺寸及質(zhì)量進(jìn)行嚴(yán)格篩選。為了檢測彎管切線方向的變形狀況,在管壁表而盡可能淺地刻入間距為1 mm的標(biāo)記線。彎曲成形后,利用精密萬能測試儀和顯微測試儀對標(biāo)距的變化進(jìn)行測量。有限元模擬的變形條件、參數(shù)與實驗完全相同,以便進(jìn)行比較和驗證。有限元模型中的模具材料為45鋼,彈性模量E=210xe9 Pa,密度P=7890 kg/m3,泊松比p=0.269;管件的材料為不銹鋼1Cr18Ni9Ti,彈性模量E=198xe9 Pa,屈服強(qiáng)度205xe9 Pa,切線模量E=1000 x e9 Pa,泊松比0.26,密度p=7900 kg/m3。
為了確定有效的有限元模擬方法,分別利用實體單元法和殼單元法進(jìn)行了模擬,在與實際彎曲實驗結(jié)果進(jìn)行初步的比較后,確定采用殼單元。模擬計算采用基于中心差分法的動態(tài)顯示時間積分的有限元算法,模型單元全部為shell163薄殼單元;管件材料模型選用經(jīng)典雙線性各向同硬化模型,根據(jù)實驗條件確定靜、動摩擦系數(shù)分別為0.11和0.09;管件一端采用節(jié)點(diǎn)剛性體約束以代替與滾動輪的連接,滾動輪和旋輪均簡化為剛性材料。模具和管件之間定義為面-面成形接觸,管子和模具表面分別為接觸面和目標(biāo)面。
管件的精確彎曲需要準(zhǔn)確掌握管件實際彎曲角度,以便于確定彎曲成形極限、管坯下料長度和縱向進(jìn)給量等工藝參數(shù)。因此,將一組實驗管件刻線后分別彎曲不同角度,測量平行于彎曲平面的中切面最內(nèi)側(cè)上彎曲起始點(diǎn)、中間點(diǎn)和終點(diǎn)圍成的角度的變化值。將實驗測得的數(shù)據(jù)與有限元模擬結(jié)果對比。數(shù)值模擬值與實驗測量值十分接近,說明了管件彎曲有限元模型建立的有效性。對比結(jié)果顯示,管件內(nèi)側(cè)上三點(diǎn)之間的角度隨著滾輪轉(zhuǎn)角增大而減小,在轉(zhuǎn)角小于40°時,彎曲角度變化較��;在轉(zhuǎn)角大于80°時,彎曲角度變化比較明顯;在轉(zhuǎn)角達(dá)到120°時,彎曲角度為最終成形角度,與滾輪轉(zhuǎn)角相差30°,彎曲角度的數(shù)值模擬值小于實測值,主要原因是數(shù)值模擬沒有考慮管材回彈的因素。
所示等效應(yīng)力最大的部位出現(xiàn)在管件彎曲區(qū)域的與滾動輪和旋輪接觸部位,其彎曲成形后部位的應(yīng)力值逐漸減小,且沿兩端方向應(yīng)力逐漸減少。管件內(nèi)側(cè)管壁的應(yīng)力值比外側(cè)管壁要大,說明內(nèi)壁受到壓應(yīng)力要大于外壁受到的拉應(yīng)力。外側(cè)管壁由于受旋輪和滾輪的共同作用而在周向和軸向上出現(xiàn)拉應(yīng)力,該拉應(yīng)力過大可能造成外側(cè)彎裂;壓應(yīng)力過大可能造成內(nèi)側(cè)起皺。
管材彎曲過程中,變形主要集中在彎曲外側(cè)和內(nèi)側(cè)。彎管形狀及等效應(yīng)變分布圖,可以看出管件彎曲內(nèi)、外側(cè)的等效應(yīng)變值明顯大于其他部位。管件外側(cè)切向伸長變形,沿管線方向的區(qū)域相對大,并且分布相對均勻,隨著離開彎曲水平中切而,等效應(yīng)變逐漸減小,在垂直于彎曲平而的中切而附近,產(chǎn)生最小等效應(yīng)變的區(qū)域略微偏向彎管內(nèi)側(cè)。
專業(yè)從事機(jī)械產(chǎn)品設(shè)計│有限元分析│強(qiáng)度分析│結(jié)構(gòu)優(yōu)化│技術(shù)服務(wù)與解決方案
杭州那泰科技有限公司
本文出自杭州那泰科技有限公司www.hwjj.net,轉(zhuǎn)載請注明出處和相關(guān)鏈接!